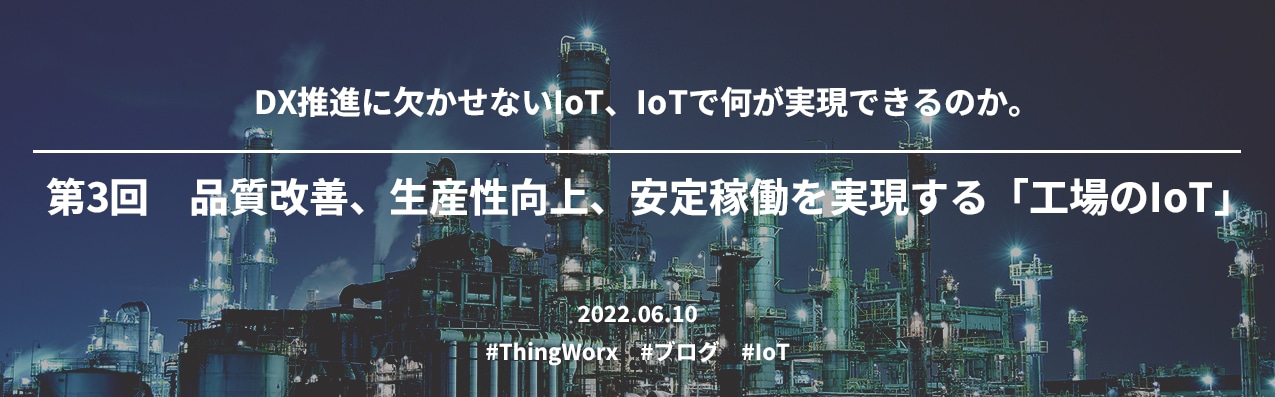
「インダストリー4.0」や「スマートファクトリー」が叫ばれるようになり、工場の生産ラインを見直そうという気運がここ10年ほどで高まってきました。工場内のさまざまな設備のデータを収集し、さらに複数の工場のデータをも一元管理し、より高度な最適化をめざす「工場のIoT」を、日立ハイテクでも多くのお客さまと進めています。第3回目は、「工場のIoT」の今について、お客さまへのコンサルティングを担当する下靖彦さんと伊東紗也佳さんに聞きました。
スマートファクトリーを実現する「工場のIoT」
―工場のDXは今、どのように進んでいますか。
伊東:はい。日本の製造業のお客さまは以前から製造プロセスを制御するシステムを導入されており、十分なデータがとれている企業が多くあります。さらに在庫データや企業の基幹システム、ヒューマンデータなどと結びつけたり、複数の工場のデータを吸い上げて一元管理し、より上位の判断につなげようという動きが進んでいます。工場の生産設備や他のシステムをつなぐ「工場のIoT」のご相談やPoCが盛んです。
―「工場のIoT」でめざす課題解決とは、どのようなことでしょうか。
下: 工場の課題は大きく3つに集約されます。1つ目は品質改善です。品質がばらつくのはなぜか、複数の工場で同じ製品をつくっているのに歩留まり率が違う原因を探りたいといった課題です。2つ目は生産性の向上です。1つの装置だけでなく、生産ラインのフェーズごとの状況を見て、生産性が向上しない要因を探るといった課題です。3つ目は、設備の安定稼働です。設備の修繕時期の把握や異常検知によって、安定した設備稼働をめざしたいといった課題です。
―製造業に強い日立ハイテクの強みが活かされるところでしょうか。
伊東: はい。弊社はじめ日立ハイテクグループは多くの工場をもっており、オペレーションテクノロジー(OT)を実践しています。「OT×IT」ができるのが私たちの強み。自社の工場で経験を蓄積しているため、製造業のお客さまからは、悩みごとや苦労していることをすぐわかってくれると評価いただいています。
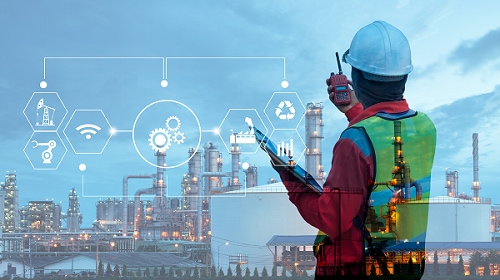
工場内の各システムのデータを、すべて一元化した事例。
―「工場のIoT」の事例を教えてください。
下: はい。あるお客さまの工場のPoC事例をご紹介します。すでにこのお客さまはDCS(分散制御システム)とMES(製造実行システム)を入れて、生産データを可視化し、効率化を図っていました。ここまでも日立ハイテクがお手伝いしてきたのですが、さらにこの上をやりたいというご要望をいただき、取り組んだ事例です。すでにDCS、MESであがっているデータと、さらに別システムであがっているデータをすべて一元化して見える化するために、IoTプラットフォーム「ThingWorx®」を導入しました。
―導入時に重視したことはどのようなことですか?
伊東:一言でいえば「収集データの一元管理とわかりやすい可視化」です。これまではDCSはDCSコンソール、MESはMESモニターの前で状況把握・診断をしていましたが、他のデータも含めて統合監視・管理モニターをThingWorxで構築しました。Webアクセスなのでユーザーさまは自席のパソコンからはもちろん、外出中にタブレットからでもこの統合モニターにアクセスできるようになりました。また、可視化のUI画面はお客さまのご要望を弊社SEがよくヒアリングしてわかりやすく見やすい画面に仕上げました。構築経験豊富なSEが全面的にお客さまをサポートすることは弊社をお選びいただく大きなメリットの1つかと思います。
―このお客さまでは、どのような成果が得られたのでしょうか。(お客さまからはどのような評価をいただいていますか)
下:これまでは「データは取れているはずだけど、どこを見るのかわからない」といった現場の声があったようですが、統合監視・管理モニターを構築したことで必要なデータや情報はThingWorxの画面でいち早くチェックでき、必要な対応も迅速にとれるようになったとお客さまから評価をいただいています。
国内外の複数工場のデータの一元管理を実現した事例。
―1つの工場だけでなく、複数工場をつなぐ事例もありますか。
伊東:はい。あるメーカーさまでは、国内のある工場で生産する製品を、国内の他の工場、さらに海外の工場でも同じように生産できるように技術を展開するため、複数工場をつなぐ工場のIoTに取り組まれました。すべての工場の生産データを「ThingWorx」のサーバーに収集して、全工場をヘッドクォーターから遠隔監視することで、品質や生産性に課題のある工場を見つけ、アドバイスを出して改善するというものです。
―導入時に重視したことはどのようなことですか?
下:「同じ生産設備を使っているのに、なぜA工場とB工場で品質、生産性が異なるのか?なぜC工場の生産設備は頻繁に不良を起こすのか?」このような課題を解決するためにお客さまと弊社SEで、どのデータを収集すべきか、データ取得周期はどのくらいにすべきか、などを徹底的に洗い出しました。工場のIoTでもすべてのデータを取得する必要はなく、収集が必要なデータと不必要なデータの選別は重要であり、最も重視したポイントです。お客さまと向き合い、必要なポイントでは時間をかけてでもお客さまととことん議論して決めていく、それが弊社の進め方です。
―本社で世界の生産拠点の情報を見ることも可能になるわけですね。
伊東:はい。ダッシュボードを使って経営コックピットをつくり、経営幹部がすべての工場の生産性やKPIを見られるようにすることも可能です。お客さまの経営効率を上げることがIoTの最終目標ですので、それを実現していきたいと考えています。
接続もアプリ開発もスピーディ。より早くスタートラインに立てる。
―「工場のIoT」を進める上で、IoTプラットフォーム「ThingWorx」を使うメリットはどのようなことですか。
下:やりたいと思ったときに短い期間で構築できることです。スクラッチ開発では2年くらいのプロジェクトになるところを、ThingWorxを使えば1カ月から半年といった短期間で構築できます。まず、装置・設備の接続が非常に早いのが特長です。実際の生産現場には、さまざまな生産装置・設備が稼働しており、データ収集に必要なインターフェースやプロトコルも異なります。そのため接続に手間と時間がかかりますが、ThingWorxは各種のOPCサーバーやPLCに対応可能な「Kepware」という制御機器用接続アプリを有しており、容易に上位のThingWorxサーバーにデータをあげることができるのです。
さらに、アプリの開発が早くできることもThingWorxのメリットです。マッシュアップビルダーというアプリ構築画面で、ドラッグ&ドロップ主体の操作で簡単にグラフや表を表示した画面構築をすることができます。お客さまがご自身で構築することも可能ですし、要件をいただいて経験豊富な日立ハイテクのSEが構築することも可能です。接続、データ管理、構築までが非常にスムーズに進むことを感じていただけるはずです。
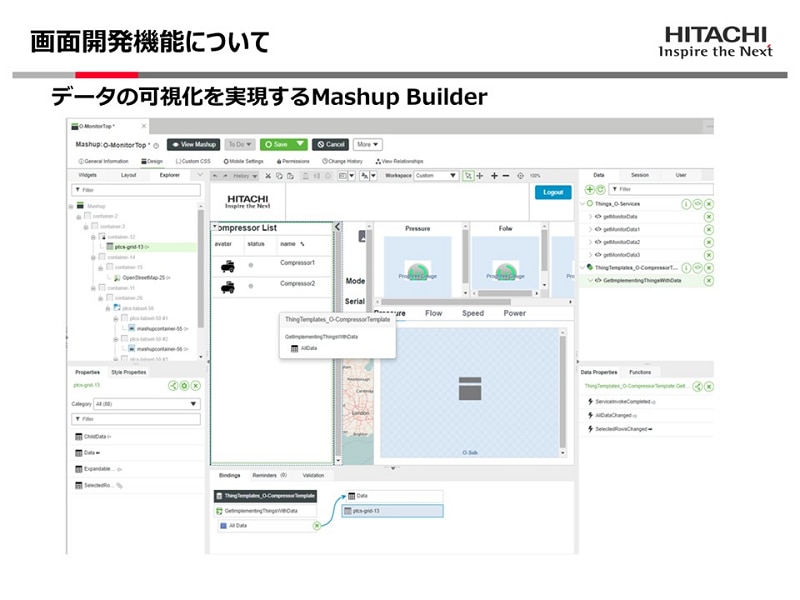
―データの利活用も見据えられるということでしょうか。
伊東:もちろんです。「ThingWorx」は拡張性も優れていますので、データを利活用して設備の異常検知ができたり、生産現場の最適化をさまざまに進めていくことができます。工場のIoTは将来を見据えた上で堅実にステップを刻み、スピーディに実行しては検証することをおすすめします。私たちに一度、ぜひお気軽にご相談いただけたらと思います。
※ ThingWorxは、PTC Inc.の米国およびその他の国における商標または登録商標です。