Product Case Studies
-
【English ver.】
【Chinese ver.】
Performing root cause analysis of faults in polymer-based products, etc.
Our company specializes in evaluation of polymer materials such as plastics. For example, we perform root cause analysis of faults such as products requested from customers by performing a set of comprehensive analyses such as analysis of mechanical properties such as tensile tests and bending tests, composition analysis such as of components, and structural observation of microscopic regions.
Among these, my division performs physical evaluation of material properties of microscopic regions from the microscale to the nanoscale, for example, by performing evaluation of the distribution of particle diameters and pores, or molecular mobility (ease of moving) of bulk polymers.Discovery of new applications to expand the services of our company
When we were asked by a customer “whether we could explain the cause when surface protection tape could not be peeled off cleanly but left residual adhesive”, we were able to explain the cause by using a Hitachi AFM that our company already owned, and this was the first trigger for introducing the AFM5300E. When the temperature dependence of the surface protection tape was measured using the frictional force measurement mode, it was found that extremely mobile components existed on the surface of tape where the residual adhesive occurred. Although AFM is often generally used for viewing surface morphology, it was found to be able to evaluate the molecular mobility of polymer surface and usable for root cause analysis of faults. Furthermore, I was involved in AFM research at my university before joining the company, and I found that I could utilize my knowledge from that time to develop evaluation of hydrophilic and hydrophobic character by chemically modifying the AFM probe. This kind of evaluation of surface properties using SPM was proposed to customers as one of the services of our company from around 5 years ago. Although it initially did not gain much penetration, the awareness grew gradually, and the second unit that we introduced in 2015 as a result was the AFM5300E.
The deciding factor for introduction was the environmental control of the AFM5300E. It continues to have the functions from the past, but also includes new functions from Hitachi to meet the new demands of our company, such as atmospheric non-exposure measurement for analyzing batteries in particular and humidity control.Utilization of various functions
Recently, force curve mapping measurement has become possible with the AFM5300E. In the evaluation of polymer alloy which has a sea-island structure, the local elasticity distribution can be evaluated by force curve mapping. Furthermore, since the AFM5300E can also change the temperature, it is possible to observe how the elasticity of the surface changes with temperature. I think that this is an extremely useful indicator.
In fact, evaluation of surface properties with SPM is positioned at our company as the last stronghold when no differences are observed from other methods. For example, I think there are often some properties that are different even though no differences can be observed by performing various analyses such as IR, and this is often resolved by using this kind of evaluation method. Our company proposes and performs analysis methods to handle the problems facing our customers. These analysis results are sometimes applied such as to improve manufacturing processes by the customers to achieve commercialization, and I feel this is very rewarding.Expectations for further functions in the future
I think that the temperature sweep has strong advantages and the temperature sweep function of Hitachi is extremely useful, and hope that technical development will continue. Although elasticity can currently be measured as temperature changes, I expect the development of a function that allows automation of evaluation while the temperature changes.
-
【English ver.】
【Chinese ver.】
Developing manufacturing processes that use microwaves—on a plant-wide scale
Our company was founded in 2007 as a venture spinoff from Osaka University; our mission is to provide microwave-based methods for making things on a plant-wide scale. In the past, conventional wisdom around the world held that manufacturing processes making use of microwaves are difficult to scale up to large sizes. We shattered this intuition in March 2014 by opening the world’s first large-scale microwave chemical plant—with annual production capacity of 3200t—at Suminoe, Osaka; this furnished real-world proof that microwaves could be used in a wide range of fields, from organic and inorganic synthesis to pharmaceutical production. Another example is graphene, a topic of current interest for which many different types of companies have growing development needs.
Using the instrument in quality testing for a new material of intense interest: graphene
Graphene is a new material whose excellent properties—extremely high electrical conductivity, transparency to visual light, extraordinary lightness and strength—make it promising for a wide range of applications, from devices to structural materials. In the past, the difficulty of mass production had been a stumbling block, but we established a method for producing graphene at volumes on the order of 10 g by applying our microwave chemical synthesis technology. Today we’re able to provide samples of adjustable thickness and weight in response to requests from our corporate clients.
Hitachi’s AFM5500M has been a crucial, irreplaceable tool for testing the quality of these samples. The AFM we were using previously, a university shared-use facility, was difficult to use—just configuring the settings took several hours. But with the AFM5500M things like cantilever switching and optical-axis adjustment are optimized automatically, so we can just focus on the measurements themselves. This is the greatest advantage of the instrument.We’re hopeful that SÆMic solutions will enable more thorough analysis
Since we installed the AFM5500M, graphene height measurements have become dramatically faster, and the instrument’s automation features ensure that anyone can acquire data under identical conditions. Even if you make a mistake while using the instrument, all you have to do is follow the instructions on the screen to obtain error-free measurements. This makes the instrument extremely easy to use.
In the solutions stage of our work involving SÆMic with the SU8000 series and the AFM5500M, we perform two different types of measurements on the samples we synthesize: SEM imaging to characterize the morphology of the sample as a whole and analyze element distributions, and AFM measurements for close-up observations of Z-axis height or physical properties such as electrical conductivity. We’ve only just installed the new instrument, but we are hopeful that combining the two types of measurement will allow us to analyze our samples in even greater depth. -
【English ver.】
【Chinese ver.】
Make accurate measurements with a single click of the mouse—even if you’re not an expert
Our company is continually creating new technologies—rooted in our core strengths of interface science—targeting a wide range of applications. The impetus for us to adopt Real Tune II was the need to make nanoscale measurements spurred by the development of our Dia Lumie translucent projector screen. However, operating an AFM turned out to be quite difficult—as we had heard might be the case—and, after seeing some hands-on examples and participating demonstrations from various vendors, we concluded that AFM was not a technology we could ever hope to master, and we almost changed our mind regarding our decision to install the instrument.
This was the point at which the folks at Hitachi explained to us that there do exist instruments that are easier to use, and we arranged—still only half expecting anything to come of it—to observe a demonstration. The only word I can think of to describe our reaction the first time we laid hands on the Real Tune II would be shocked! As we clicked the Auto button on the console and watched the instrument proceed to make the measurement by itself, we started to think, “This is actually something we can use.”The ease of using the instrument creates an ever-expanding breadth of applications
Originally, we used the instrument to observe the dispersion and condensation of nano-diamonds, but since then the range of things we do with the tool just seems to keep growing—from cross-sectional surfaces of hairs, to processed fibers, new materials, and data on films that can’t be observed via SEM. The reason we can use the system for such a broad spectrum of applications is that it automatically adjusts the measurement settings appropriately for each sample, making it extremely easy to use. We’ve also become quite familiar with the menus and windows. As far as resolution is concerned, it obtains images of the same quality as TEM images, which is more than adequate performance for our needs. Another key advantage is the ability to use the instrument in ambient conditions, allowing us to make measurements of samples close to their natural state.
We use SIS Mode to make measurements in cases requiring greater accuracy. Our company manufactures things like cosmetics, so it’s really convenient that we can make accurate measurements of samples with high water content.Excellent customer support allows us to use the instrument with confidence
Before we installed this instrument, our company lacked AFM experience, so when we first started seeing images we didn’t even know if they had been measured correctly. At that point it was very reassuring that we could email our images to Hitachi support and receive helpful expert advice—such as “the probe might be experiencing friction.” We’re grateful for the extensive support framework that makes it easy to ask questions whenever there’s something—even something minor—that we don’t understand.
-
【English ver.】
【Chinese ver.】
The ease of controlling environmental conditions was the decisive selling point for us
We’re a company that conducts morphological observations, surface analysis, composition analysis, and other types of measurements on a wide variety of organic and polymer materials. In particular, my group is currently responsible for scanning probe microscope techniques for surface analysis.
We installed the AFM5300E in 2010, and one of the major reasons we chose this instrument was the simple and easy environmental controls it offered. For companies like ours that accept requests for outsourced analytical work on a contractual basis, the fact that the AFM5300E allows analysis under all types of environmental conditions makes it extremely convenient, and in the 7 years since we acquired the instrument we’ve used it to characterize the physical properties of a huge variety of samples.The fact that the customer support system allows us to ask our questions directly is very reassuring.
We’ve found the customer support system to be quite reliable.
For the most part, the AFM5300E is an instrument that rarely malfunctions—but we’re still grateful for the speedy and thoughtful response we’ve received in cases where we caused our own problems by using the instrument incorrectly. The fact that we can ask questions directly by e-mail or phone whenever we aren’t sure about something—that was one of the major reasons we decided to go with this model.
I previously learned the basics of AFM measurements from lectures at a Hitachi-organized seminar, and I still remember being struck by how thoroughly the presenters understood their subject. Ever since, I’ve continued to be impressed by the presentations at seminars and advanced courses pointing out an ever-broadening range of applications. Hitachi offers seminars and practical-training courses quite frequently, and we’re always encouraging our younger staff members to participate to broaden their skills. Of course, the only way to learn to use the instruments is actually to use them in practice, but Hitachi’s educational opportunities are excellent opportunities to entrench one’s understanding of the theoretical side of things.SIS mode offers a whole new level of stability—even for samples that are difficult to measure
An attractive feature of SIS mode is that it allows stable, reliable measurements even for soft, sticky samples—and for extremely hard samples as well. For example, we’ve been able to study the surfaces of soft samples like dielectric polymers at high resolution with good accuracy. Also, for analyzing hybrid materials involving mixtures of components of varying hardnesses, conventional instruments always had problems with reproducibility, but SIS mode allows stable measurements every time. This is incredibly helpful.
For the clients who trust us to handle their contract analysis work, the absolute number-one requirement is reliable data. The fact that SIS mode always allows us to acquire stable data is a huge advantage. Another nice feature is that, because the probe tip is not dragged along the surface in SIS mode, the tip suffers only extremely minimal damage, helping to keep operating costs under control.
Product lineup
Hitachi AFM will prove useful at any stage
By application
Automation / Ease of use
High accuracy / High resolution
- High-accuracy measurements of slanted surfaces with a steep slope
- High-accuracy measurements without damaging samples
- High-resolution measurements in a vacuum
- Stable and accurate measurements during sample heating and cooling
- High-accuracy topography measurements
- High-sensitivity MFM measurements in ambient or vacuum environments
- Humidity control / observations in liquid
Physical property measurements /
Environmental Controls
- Measurements of work functions in ambient or vacuum environments
- Observations of dopant distribution
- Quantitative measurements of elastic modulus
- Observations of structural changes in a vacuum
- Enabled true observations of topography and other physical properties
- Enabled quantitative measurements during sample heating and cooling
This section introduces applications (actual measurement cases) for scanning probe microscopes (SPM/AFM).
Information for product users
This section offers information aimed at customers who use our scanning probe microscopes.
For first-time users
Related topics
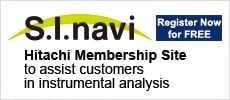
“S.I.navi” is Hitachi Membership Site for analytical instruments users.
“S.I.navi” provides helpful information for daily analysis.